CBBMACHINE Safety Chuck Designs for Smarter Shaft Handling
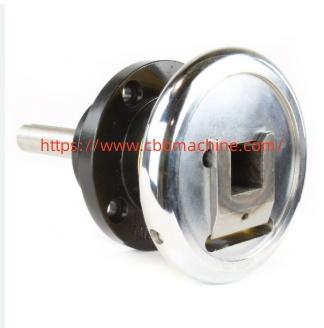
In industrial winding and unwinding operations, the role of a Safety Chuck in ensuring quick coupling and secure shaft engagement is indispensable for productivity and operator protection. This mechanical device acts as a reliable interface between the motor and the shaft, allowing for rapid loading and unloading of reels without the need for complicated tools or excessive downtime. It minimizes setup time and increases safety by automatically locking the shaft in place once inserted and rotating, which reduces the risk of operator injury from unsecured loads.
Safety chucks are commonly used in various industries including printing, packaging, plastic film, textiles, and paper converting. Their ability to accommodate rotary motion while holding the shaft firmly in place makes them essential for any high-speed roll-to-roll machinery. Depending on the application, safety chucks can be configured in foot-mounted or flange-mounted styles to match specific machine setups.
One of the key advantages of using these chucks is their compatibility with different types of shafts and expanding devices. Whether it's a square bar, triangle, or round shaft, modern chucks can be customized to suit various end-user requirements. Additionally, they can be integrated with mechanical or pneumatic expanding shafts, improving overall control during winding operations. Their sturdy construction ensures long service life, while easy-access inserts make maintenance or replacement convenient.
A typical safety chuck is designed to disengage automatically once the machine stops rotating, preventing any rotational motion that could lead to damage or harm. Advanced models offer features such as wear-resistant inserts, position locking, and axial load handling to enhance operational efficiency. Furthermore, some chucks are fitted with sensors to monitor rotation and position, aiding in process automation.
Routine inspection and preventive maintenance are recommended to keep these components functioning optimally. Checking the insert condition, ensuring proper lubrication, and verifying shaft engagement are all simple steps that can significantly prolong the chuck’s lifespan. When replacements are necessary, the modular design of modern chucks allows for swift insert swaps without removing the entire unit.
In conclusion, the implementation of a reliable chuck system supports smoother operations, increased safety standards, and reduced mechanical wear in automated production lines. By integrating such components, manufacturers not only enhance performance but also ensure compliance with industrial safety protocols. To explore more about the technology and models available, visit https://www.cbbmachine.com/news/industry-news/safety-chucks-function-types-maintenance-and-more.html.